San Motion R
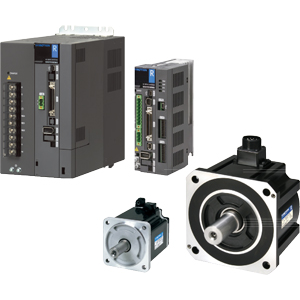
Product Details
High-performance AC servo systems consisting of servo amplifiers with advanced vibration suppression and highly efficient servo motors. High resolution encoders improve trajectory accuracy and position repeatability by dramatically improving responsiveness. By providing optimal performance, this is a key component for reducing cycle time and improving production efficiency.
Features
Servo Motor
R2 Servo Motors
R2 Servo Motor wide inertia lineup. They are ideal for use in equipment such as robots, injection molding machines, and general industrial machinery.
R1 Servo Motors
R1 Servo Motors are low inertia servo motors with low inertia and high acceleration for agile operation. These are ideal for inspection equipment.
R5 Servo Motors
R5 Servo motors are medium inertia servo motors that are ideal for smooth operation.
Servo Amplifier
More evolved AC servo amplifiers that provide improved basic performance including high responsiveness, and pursue eco-efficiency and ease of use. More evolved AC servo amplifiers that provide improved basic performance including high responsiveness, and pursue eco-efficiency and ease of use.
Batteryless Absolute Encoder Model No. HA035
The encoder has no batteries, which have limited service lives, so it can be maintenance free. It is ideal for transportation equipment and industrial equipment needing high accuracy, such as machine tools, injection molding machines, and robots.
Batteryless
Battery replacement maintenance is not needed, so manpower and time are significantly reduced.
High resolution
The number of divisions in a revolution is up to 8,388,608 (23 bit).
This enables fine equipment control.
Environmental durability
The operating temperature range is from -20°C to +105°C
The environmental vibration limit is a maximum of 147 m/s2 (15 G).*1
They can be used in harsher environments than our conventional products.
*1 The operating temperature and environmental vibration when mounted on a servo motor depend on the servo motor’s specifications.
Shorter cycle time achieved through high-speed positioning control
The 3E Model has a speed frequency response of 2.2 kHz, approximately twice that of our conventional product.*2
In addition, position settling time has been shortened to 1/3. A function for switching between trajectory control and positioning control in real time has been incorporated to significantly reduce the cycle time of the device.
*2 For amplifiers with capacities from 10 to 50 A. Compared with our conventional AC servo amplifier, SANMOTION R ADVANCED MODEL.
Improved control accuracy
Gain can be increased by increasing responsiveness. It is equipped with a function for suppressing micro-vibration at settling time, an adaptive notch filter for suppressing mechanical resonance, and a feed-forward vibration control function. The 4th order notch filter of our conventional product has been upgraded to 5th order for finer vibration control. *3
Highly-accurate machine tool feed-axis control significantly improves processing quality.
*3 Compared with our conventional AC servo amplifier, SANMOTION R ADVANCED MODEL.
Improved safety performance through the Safe Torque Off function
With the improved Safe Torque Off (STO) function, the 3E Model conforms to international standards
IEC 61508: SIL 3 and ISO 13849-1: PL=e. They are sufficiently reliable to be used in devices requiring high safety.
SANMOTION R ADVANCED MODEL AC Servo Systems
High performance and small AC Servo Systems
With the excellent control technologies of the SANMOTION R series maintained, the SANMOTION R ADVANCED MODEL has models with various functions including the next-generation EtherCAT fieldbus. The disturbance suppression characteristics and robustness required for servo systems can be realized to a higher degree, contributing to reduced cycle time.
Compact design with reduced height and width
The size of the housing was up to 15% smaller than that of conventional SANMOTION R series products. This contributes to control board miniaturization and equipment space-saving, and saves resources.
Products conforming to international safety standards
A lineup featuring the STO function (safe torque off function) has been developed to improve safety. Motor torque can be cut safely by forcibly turning off the PWM control signal with a duplexed circuit breaker, Defined in IEC 61800-5-2: Safe Torque Off, and IEC 60204-1: Stop Category 0). Also, the IEC 61508/IEC 62061, SILCL 2 and ISO 13849 1: Cat 3, PL = d safety standards were acquired.)
High speed peak torque increased by 15%
Using magnetomotive phase difference angle control and excitation current optimization techniques, maximum instantaneous torque is improved by 15% even when used with the same model of motor.
Model following vibration suppression control
SANMOTION R ADVANCED MODEL contains model following vibration control The signal from the top enters the model control system, and the model control system output is sent to the normal feedback control system.
When model-following vibration suppression control is used, settling time after decelerating to a stop is shortened to half that of conventional vibration suppression control.
Equipped with the EtherCAT open serial communication standard
We offer a lineup of SANMOTION R ADVANCED MODEL amplifiers with EtherCAT interfaces. EtherCAT is a high-speed open field network with a 100 Mbps communication speed, which uses Ethernet for industrial applications. Because communications are serial, it contributes to decreased wiring between units. With accurate synchronization and openness, this field bus is ideal for future servo systems.
SANMOTION R 14 mm sq. AC Servo Motor
High performance and small AC Servo Systems
We have achieved high precision control with industry leading miniaturization. It is suitable for applications such as chip mounter heads, small XY tables, semiconductor manufacturing equipment, inspection equipment, and other equipment that requires reducing the space between axes.
Industry’s smallest mounting angle
By introducing new winding techniques, we have achieved a flange size of 14 mm × 14 mm, the industry’s smallest class*4. It is ideal for devices with limited space for mounting motors, and contributes greatly to equipment miniaturization.
*4 Based on our own research, as of March, 2009.
High-precision positioning control with high 17-bit resolution
The newly developed 17-bit (131,072 division) high-resolution, ultra-compact absolute encoder is equipped with high-precision positioning control and low speed range stability.
Also, a feature of absolute encoders is that they can shorten startup times and quickly recover from power failures.